저번 전극공정에 이어 조립공정입니다. 파우치 타입의 조립공정은 '노칭-라미네이션-스태킹&폴딩-포장'의 순서로 구성되어집니다. 각형은 극판에 회전을 주어 와인딩하는 방식인 젤리롤 방식을 사용합니다. 그리고 캔에 젤리롤을 넣습니다. 하지만 최근, 캔 타입에서 스태킹 방식을 도입하고 있습니다. 앞으로 각형의 공정은 파우치와 비슷해질 것입니다.
대표적으로 젤리롤 방식으로 배터리를 제조하던 삼성SDI가 헝가리 양산라인에 스태킹 방식을 도입한다고 밝혔습니다.
https://m.etnews.com/20200605000043
삼성SDI 전기차 배터리 '스태킹' 방식으로 만든다…헝가리에 양산 라인 구축
삼성SDI가 전기차 배터리 제조 방식에 큰 변화를 준다. 고밀도·고용량 배터리 생산을 위해 기존 와인딩 방식 대신 스태킹 공정을 도입하기로 했다. 스태킹 방식은 LG화학과 SK이노베이션이 전기��
www.etnews.com
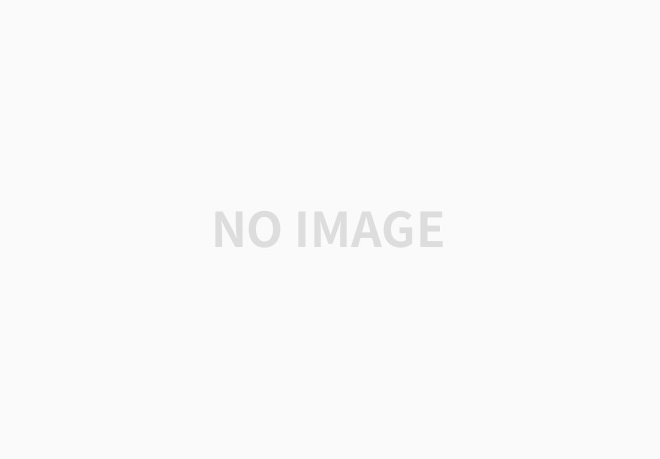
이 그림은 앞서 말씀드렸듯이 파우치 방식의 공정입니다.
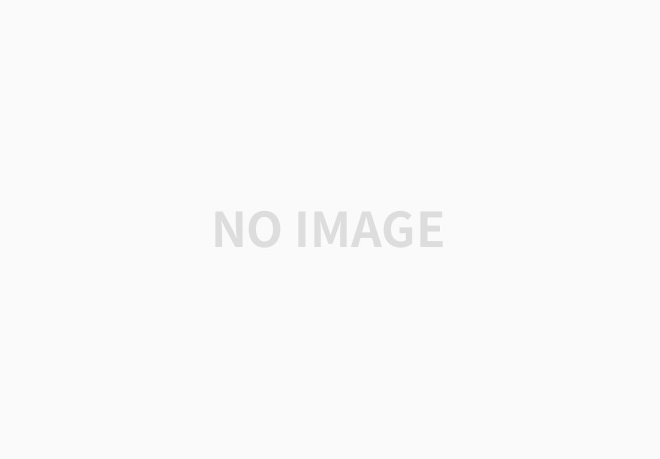
Toray에서 보여주는 배터리 제조 프로세스 입니다. 파우치형 제조 방식입니다. 이 그림을 보시면 전극 공정에서 코터, 활성화 공정이 가장 큰 부피를 차지하는 것을 볼 수 있습니다.
2. 조립공정
조립공정 | 공정 | 업체 | 기타 |
노칭 | 필옵틱스, DA테크놀로지, 엠플러스 등 | ||
라미네이션 | 나인테크, DA테크놀로지 등 | ||
스태킹&폴딩 | DA테크놀로지, 엠플러스, 이노메트리 등 | ||
포장 | 엔에스, 엠플러스 등 |
1) 노칭
전극공정에서 슬리팅된 것을 배터리 크기에 맞게끔 노칭(자르는)하는 작업입니다. 노칭은 레이저로 할 수 있습니다.
노칭은 배터리 소재에 동박과 알루미늄박을 붙이는 전극 공정 바로 뒤에 위치합니다. 배터리 셀을 구성하고, 포장해 제품으로 만드는 조립 공정의 첫 번째 단계입니다.
1-1) 장비 설명
*필옵틱스 노칭설비(제품특징)
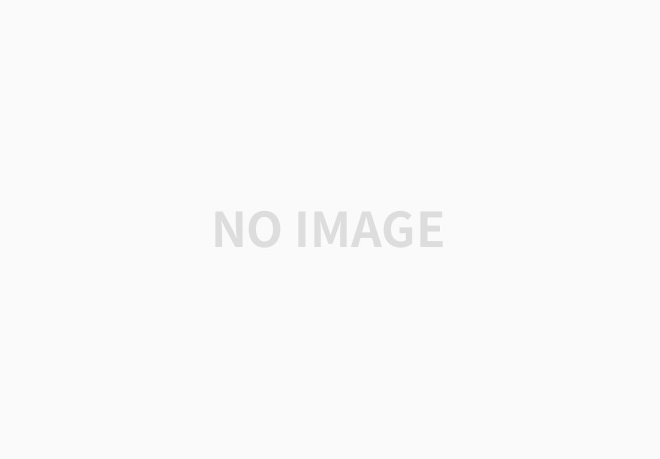
*디에이테크놀로지 노칭설비(제품특징)
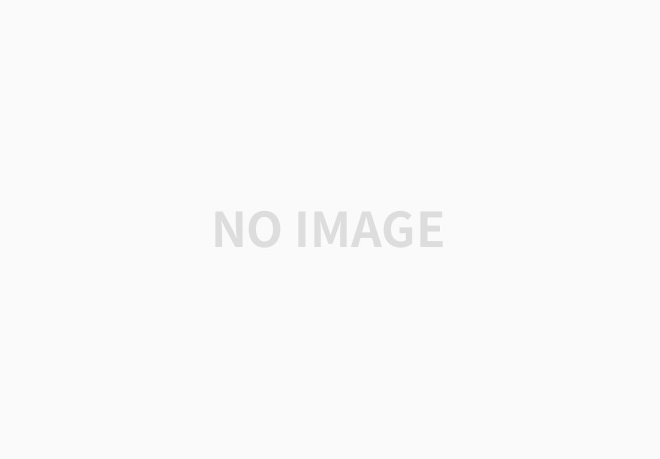
1. Press Notching M/C (Roll to Roll)
Roll 형태로 Winding된 음극/양극 전극을 Punch Press로 Tab 및 Bottom에 일정 형상을 Notching 후 Rewinding 하는 자동화 설비
- 금형(Press) Mechanical Notching 적용
- 전극의 사행방지 및 Tension 자동조절
- 초 정밀 Feeding System 적용
- Notched된 전극 Dimension Vision 검사
- 스크랩 및 이물제거
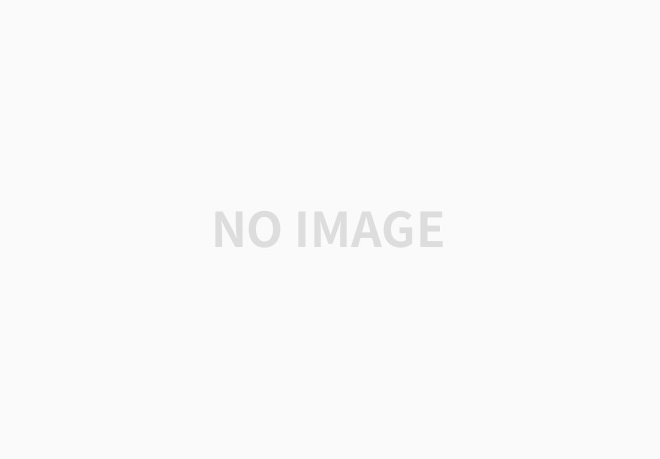
2. Press Notching M/C (Roll to Roll)
Roll 형태로 Winding된 음극/양극 전극을 Laser 적용하여 Tab 및 Bottom에 일정 형상을 Notching 후 Rewinding하는 자동화설비
- Laser Optical Notching 적용
- 전극의 사행방지 및 Tension 자동조절
- 초 정밀 Feeding System 적용
- Notched된 전극 Dimension Vision 검사
- 스크랩 및 이물제거
- 자동 Reel 교체 장치 적용
2) 라미네이션
레미네이션을 하는 이유는 극판 자체에 안정감을 가지고 이물질 투입을 방지하는 기능입니다. LG의 경우 자동차 배터리에서 수명을 늘리게 하는 기능도 합니다.
2-1) 장비 설명
*디에이테크놀로지 라미네이션설비(제품특징)
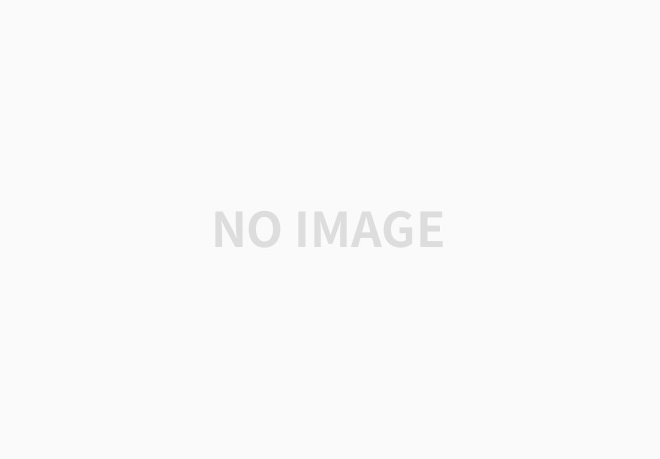
Notching 된 전극과 분리막을 열융착시켜 Bi-cell을 만들고 검사 후 Magazine에 적재하는 설비
- 정밀 전극, 분리막 사행 조정
- 고속 실시간 위치 연산&보정 Align System(자체 Program 개발)
- 고속 정밀 Side Cutting 적용
- 전극 및 분리막 Lot ID 관리
- 완성된 Bi-cell 검사
- 적재 완료 Magazine 자동 교체
*나인테크 라미네이션설비(제품특징)
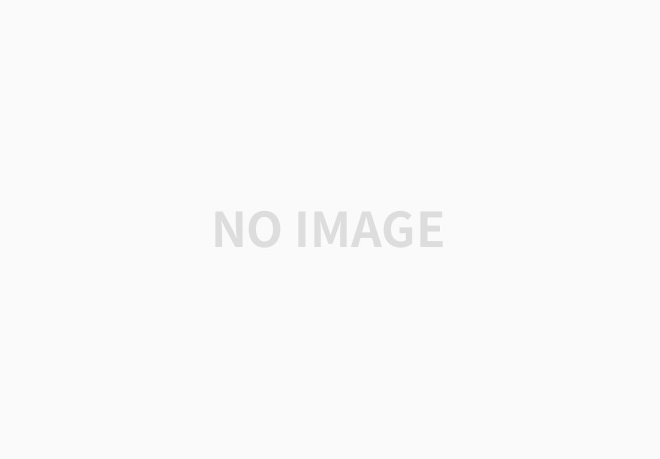
전자동화 소재의 공급 및 배출을 제외한 전 공정 연속 자동 생산
- 고생산, 고신뢰성: 연속 생산 중
- 보정 및 검사기능을 통한 높은 생산
3)스태킹&폴딩
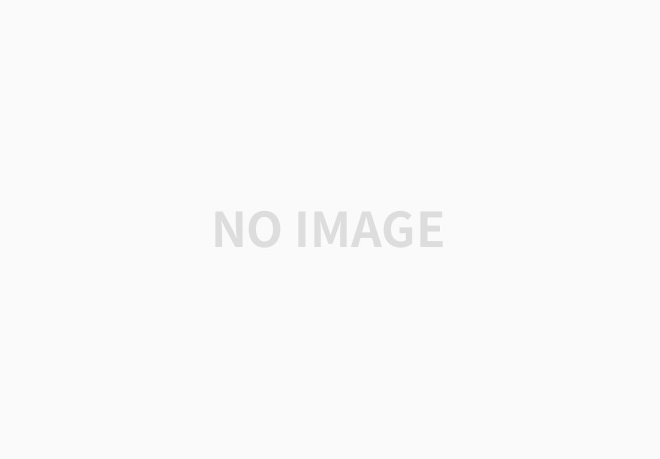
스태킹 공정은 노칭과 라미네이션을 지난 제품을 적층하는 방식으로 쌓아주는 공정입니다.
스태킹 방법은 공간활용이 잘되어 와인딩 방식의 배터리보다 배터리 용량이 높다는 장점이 있습니다.
스태킹 방식은 생산성을 높이기 위해 고속, 고정밀 스태킹 작업이 필요합니다.
(출처 - metnews)
3-1)장비 설명
*엠플러스 스태킹설비(제품특징)
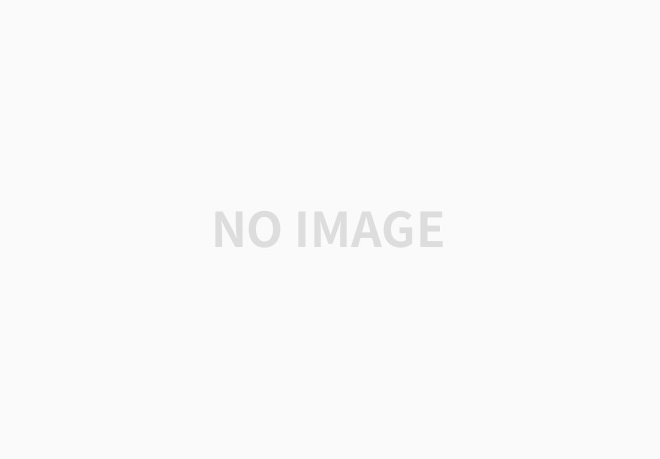
- Vision 얼라인 기능 적용으로 정확한 얼라인이 가능하며, 불량 극판의 자동검출 및 배출 가능
- Barcode Scanning 기능 적용으로 극판 생산 이력 추적 가능
- Double arm Stack 방식으로 생산 대기시간 최소화
- 극판 이재시 이매분리 기능 설치로 NG 극판 발생 최소화
3-2)제조 방식
지그재그식 스태킹 장비
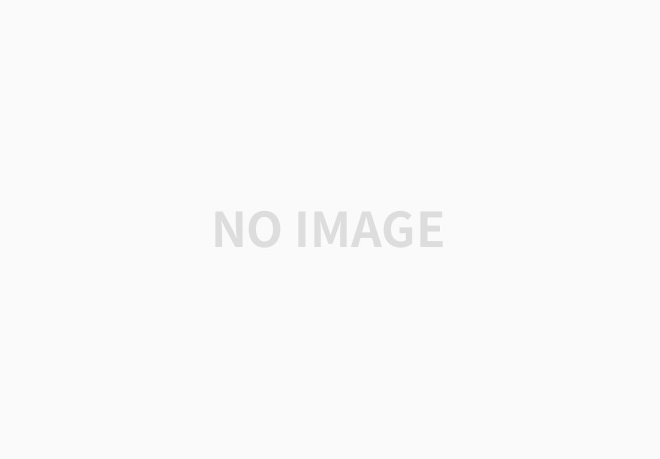
와인딩 스태킹 장비
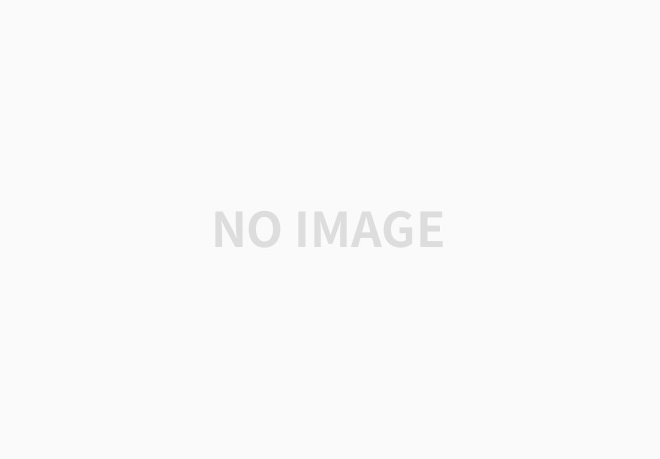
매듭 스태킹 장비
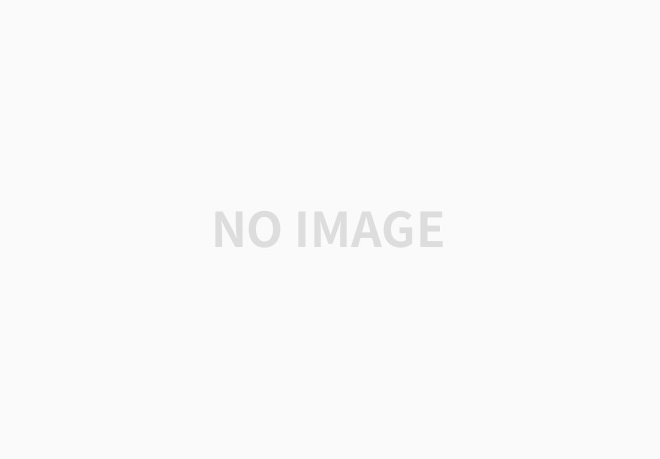
최근 SK이노베이션이 Z-스택 방식을 도입해 생산성 30% 향상을 이뤘다는 발표가 있었습니다. 헝가리 코마롬과 미국 조지아 배터리 신공장에 대용량·초고속 기술을 활용한 신공정으로 극을 낱장으로 재단 후 분리막과 번갈아 쌓는 ‘Z-스태킹(Stacking)’을 검토중입니다.
업계의 한 관계자는 “배터리 생산량을 일정 수준으로 높여야 경쟁력을 확보할 수 있기 때문에 공정 도입은 필수적”이라며 “해당 신공정은 파나소닉, CATL이 도입을 검토 중이어서 SK이노베이션뿐 아니라 LG화학, 삼성SDI도 활용 방안을 고민할 수 있다”고 전했습니다.
출처 : 전자부품 전문 미디어 디일렉(http://www.thelec.kr)
4)포장
파우치의 경우 양 면에 파우치를 씌워 열을 가해 패킹을 합니다. 일반적으로 진공포장과 같다고 볼 수 있습니다. 순서로는 파우치를 눌러 형태를 만들고, 내부의 공기를 뺍니다. 압착을 해 열을 가한 후 검사 과정을 거칩니다.
4-1)장비 설명
*엠플러스 패키징설비(제품특징)
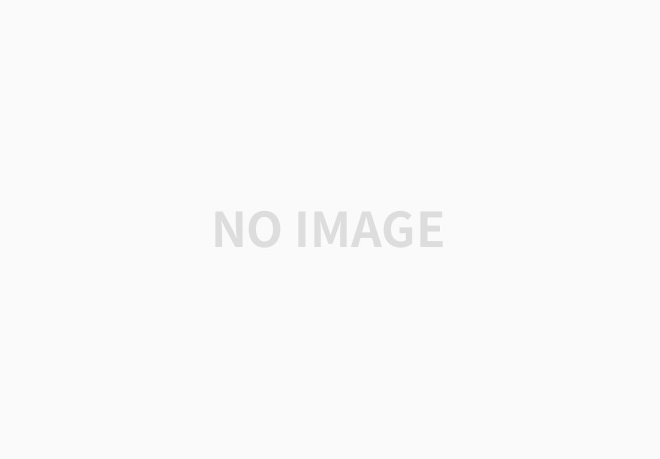
- 온도 보상 시스템 적용으로 균일한 파우치 Forming 품질 구현
- 대용량 고속 주액기의 적용으로 설비의 생산효율 극대화 및 전지의 오염을 방지
- 고성능 진공펌프 및 밀폐형 챔버 적용으로 LEAK최소화
- 실시간 비젼 검사 적용
- Fill tube 적용으로 고속주액 시스템 구현
*엔에스 패키징설비
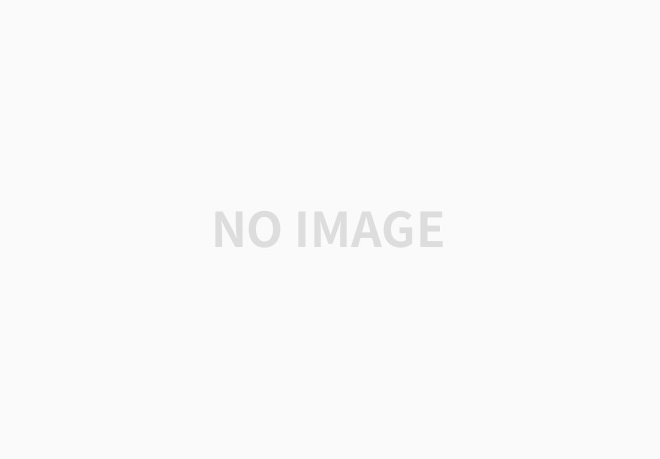
여기까지 조립공정의 설명이었습니다.
.
.
.
감사합니다.
.
.
.
'2차전지 산업 > 제조 기술' 카테고리의 다른 글
배터리 제조 프로세스 4. 활성화공정 (2) | 2020.08.04 |
---|---|
배터리 제조 프로세스 2. 전극공정 (0) | 2020.07.01 |
배터리 제조 프로세스 1. 배터리 타입(파우치형, 각형, 원통형) (2) | 2020.06.25 |
리튬이온 배터리 기초 5. 분리막이란? (0) | 2020.06.15 |
리튬이온 배터리 기초 4. 전해액이란? (0) | 2020.06.12 |