오늘은 배터리 공정 프로세스에 대해 알아보도록 하겠습니다. 배터리는 크게 1. 전극공정, 2. 조립공정, 3. 활성화 공정으로 나뉘어 집니다. 각 배터리의 타입과 배터리 제조사별 차이를 가지고 있습니다. 우선, 각 배터리 타입에 대해 알아보도록 하겠습니다.
배터리 타입
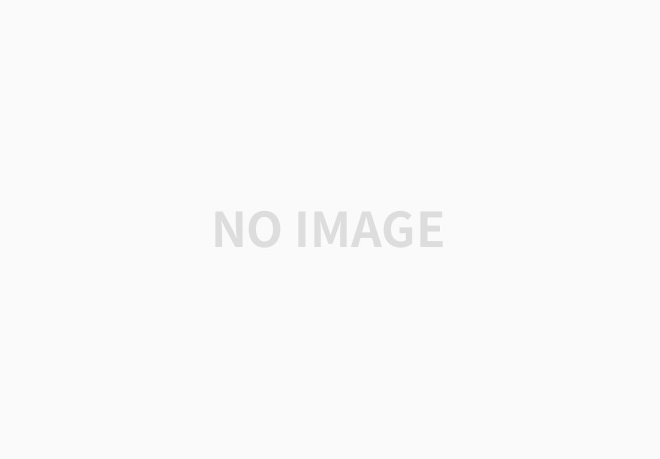
배터리는 파우치형, 각형, 원통형으로 나눠집니다. 각 배터리는 특성의 차이를 가지고 있습니다. 각 타입은 장, 단점이 명확히 나뉘어 집니다. 그렇기에 '어떤 배터리가 좋다'라고 쉽게 말할 수 없는 상황입니다. 이런 상황은 제조사별로 나누어보면 더 쉽게 알 수 있습니다.
Top10 기업의 배터리 타입을 살펴보겠습니다. 각형 배터리를 사용하는 기업은 CTAL, BYD, 삼성SDI, CALB, CATL-SAIC입니다. 파우치형 배터리를 사용하는 기업은 LG화학, AESC, SK이노베이션입니다. 원형 배터리는 파나소닉이 유일합니다. 각형 6 : 파우치 3 : 원형 1의 비율을 가지고 있습니다. 점유율 상으로 보면 각형이 우세한 상황입니다.
제조 프로세스를 거쳐 생산되는 배터리를 셀이라고 합니다. 이러한 셀을 적정 숫자에 맞게 묶은 것을 모듈, 그리고 모듈을 묶은 것을 팩이라 합니다. 전기차는 많은 에너지가 필요하기에 이런 방식을 사용하고 있습니다.
셀은 부피당 용량이 높아야 효율이 좋습니다. 주행 중 충격과 급격한 온도 변화를 견딜 수 있는 내구성과 안정성이 필요합니다. 내구성과 안정성을 위해 하나의 프레임으로 묶는 것을 모듈이라고 합니다. 모듈을 여러개 모아 온도와 전압을 관리해주는 BMS(Battery Management System)를 추가하면 팩이 됩니다.
타입별 설명
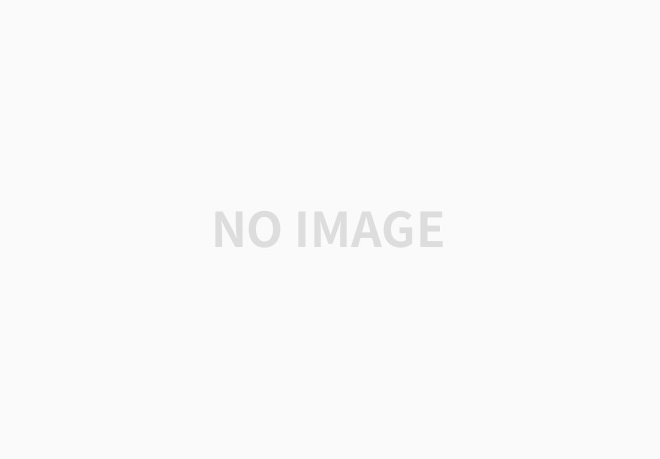
1. 각형 배터리
각형 배터리는 사각형 틀을 이용해 패키징한 형태입니다. 삼성SDI와 CTAL의 주력 품목입니다. BMW의 순수전기차 i3와 플러그인 하이브리드 i8이 삼성SDI의 각형 배터리를 사용했습니다.
각형은 알루미늄 캠으로 만들어 내구성이 좋고, 팩 조립에 유리합니다. 대량 생산시 공정단계가 파우치형보다 간소해 비용이 절감됩니다. 하지만 금속 케이스로 무게가 많이 나가고 열 방출이 어려워 따로 냉각 장치가 필요합니다.
결정적인 문제로, 파우치형보다 에너지 밀도가 낮습니다. 제조 방식에서 와인딩(Winding) 기법을 사용하기 때문입니다. 돌돌말아 제조를 하기 때문에 캔 형 모서리의 빈 틈을 활용하기 힘듭니다. 이것을 젤리롤이라 부릅니다.
현재는 와인딩 방식보다 스태킹 방식을 도입하고 있습니다. 파우치형에 사용되는 스태킹은 소재를 층층이 쌓는 적층 방식입니다. 최적 공간 활용이 가능해 에너지 밀도를 높이는데 좋습니다.
최근 각형의 기술이 좋아지고 있습니다. 각현은 Cap Assembly 라는 기능이 있어 안전장치를 더 설치할 수 있습니다. 대표적인 것이 Vent입니다. 내부에 가스가 찼을 때 터지는 기능을 막기위해 Vent를 장착합니다. 파우치는 이런 장치를 넣을 수 없습니다.
파우치가 각형보다 뛰어났던 이점은 스태킹 방식으로 에너지 밀도의 손실이 없다는 점입니다. 하지만, 각형도 스태킹 방식을 도입하자 품질에서 파우치를 능가하는 상황이 발생합니다. 물론 원가 상승이 예상됩니다. 이러면 파우치의 장점을 모두 흡수하고, 각형이 파우치 대비 강한 안전성을 가질 수 있습니다.
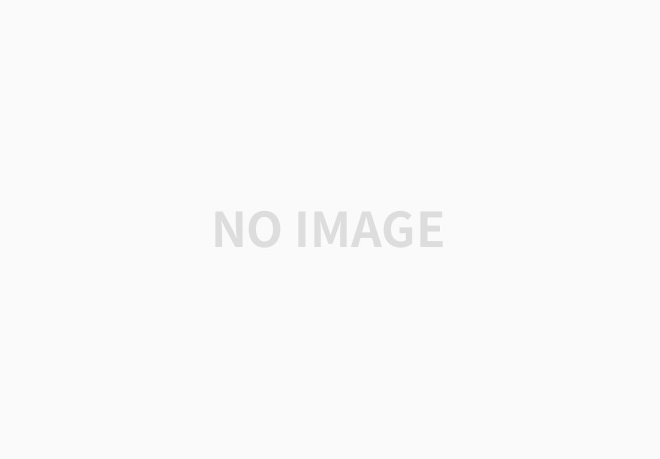
2. 파우치형 배터리
파우치형은 LG화학과 SK이노베이션이 주력으로 제작하고 있습니다. 배터리 소재를 층층히 쌓고 패키징 하기 때문에 내부에 빈 공간이 없습니다.
각형과 원통형에 비해 설계 자유도가 높습니다. 긴 모양, 짧은 모양, L 모양 등 전기차 업체의 다양한 요구 사항에 대응이 가능합니다. 그래서 LG화학은 파우치 제작 기법의 특허를 가지고 있습니다. 특히, 내부 극판을 잘라 적층하는 방식으로 내부의 변형이 없는 품질을 자랑합니다. 현대 코나와 아이오닉 일렉트릭, 재규어 i 페이스, 쉐보레 볼트 EV, 볼보 XC60 플러그인 하이브리드 등 많은 업체가 사용하고 있습니다.
알루미늄 파우치로 패키징 하기 때문에 무게가 가볍고 에너지 밀도도 높습니다. 에너지를 장기간 안정적으로 낼 수 있는 장점도 있습니다. 하지만 각형과 원통형에 비해 생산 단가가 비싼 것이 약점입니다.
하지만 이것도 신공법을 통해 보완하고 있습니다. SK이노베이션의 Z-스태킹 공법을 활용해 생산성 향상을 이루고 있습니다. 이처럼 배터리 산업을 계속해서 발전하고 있어 새로운 공정과 기법이 큰 변화를 가져올 것입니다. 현재 캔형이 좋다, 파우치형이 좋다 말하기 어려운 상황입니다.
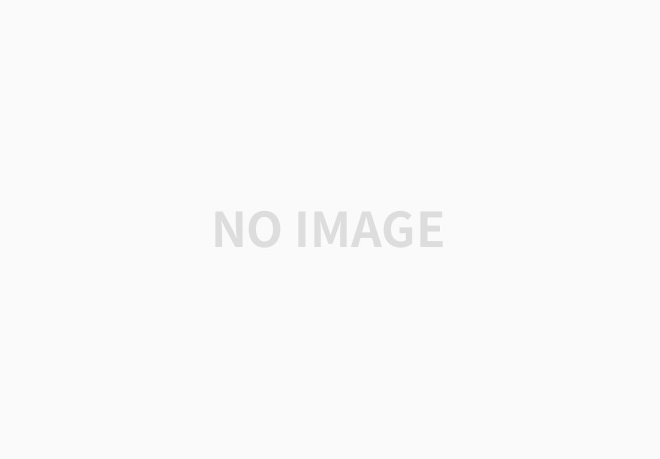
3. 원통형 배터리
가장 쉽게 볼 수 있는 형태입니다. 각형, 파우치형과 달리 표준화 됐다는 특징이 있습니다. 전기차에 주로 사용 중인 원통형 배터리는 지름 18mm, 길이 65mm의 는 '18650' 규격입니다.
본래 노트북 배터리 위주로 시장을 형성해 온 가장 전통적인 방식의 배터리이기 때문에 가장 싸고 수급 안정성이 돋보입니다. 다만 각형과 마찬가지로 젤리롤 와인딩 방식이기 때문에 비교적 에너지 밀도가 낮습니다.
일본 파나소닉의 주력 품목이며 미국의 테슬라가 대표적인 원통형 배터리 탑재 브랜드입니다. 모델S 90D는 7000개가 넘는 18650배터리 셀을 사용합니다. 최근에는 용량과 크기를 업그레이드 한 21700 모델이 주목 받고 있습니다. 테슬라 모델3가 21700 배터리셀 약 3000개를 탑재합니다.
원통형 배터리는 전기차 배터리 시장에서 가장 주목 받는 모델입니다. 시장조사업체 SNE리서치에 따르면 2017년 글로벌 출하량 70GWh였던 원통형 배터리 시장은 올해 125GWh, 내년 150GWh로 급성장 할 것으로 추측됩니다.
최근 차세대 테슬라라고 불리는 미국 루시드 모터스가 하반기 출시할 루시드 에어에 21700 모델을 탑재한다고 밝혔습니다. 그리고 LG화학이 2023년까지 단독으로 해당 제품을 공급하는 계약을 따냈습니다.
원통형 배터리는 비단 전기차 뿐 아니라 전동스쿠터 같은 경전기 이동수단 등에서 수요가 발생하고 있습니다. 때문에 각형에 주력했던 삼성SDI나 파우치형의 LG화학도 원통형 배터리 시장 공략에 나서고 있습니다.
삼성SDI는 지난해 3월부터 중국 텐진 공장을 통해 월 200만셀 이상의 21700 모델을 양산 중입니다. LG화학은 난징 공장의 생산량을 두 배로 늘려 18650, 21700 모델을 생산하고 있다. 연간 10억셀에 육박할 것으로 보입니다.
.
.
.
앞서 말씀드렸듯이, 최근 각형 배터리 업체들이 와인딩(Winding) 방식 대신 스태킹(Stacking) 공정 적용에 나서고 있습니다. 와인딩 방식은 소재를 엮어서 돌돌 말아 젤리롤을 이용한 것입니다. 원통형 배터리처럼 금속 캔에 배터리 소재를 돌돌말아 넣는 것입니다.
이러한 방식은 내부 공간을 100% 활용하기 어렵습니다. 귀퉁이에 남는 공간이 생기기 때문입니다. 충반전을 반복하면 젤리롤이 변형되는 스웰링 현상도 나타날 수 있습니다. 그동안 젤리롤은 생산성이 더 높고, 단가가 낮기 때문에 활용됐습니다. 하지만, 배터리의 용량이 중요해진 만큼 스태킹 방식으로의 전환이 되고 있습니다.
.
.
.
감사합니다.
'2차전지 산업 > 제조 기술' 카테고리의 다른 글
배터리 제조 프로세스 3. 조립공정 (1) | 2020.07.02 |
---|---|
배터리 제조 프로세스 2. 전극공정 (0) | 2020.07.01 |
리튬이온 배터리 기초 5. 분리막이란? (0) | 2020.06.15 |
리튬이온 배터리 기초 4. 전해액이란? (0) | 2020.06.12 |
리튬이온 배터리 기초 3. 음극재란?(쉬운 내용) (0) | 2020.06.08 |